The star discharge valve is an unloading device designed cement equipment for discharge points that operate under negative pressure. It conveys materials using a rotating rotor. This design provides a sealing effect that prevents air from being drawn in during pneumatic conveying, ensuring normal discharge.
Features of Star Discharge Valve
- Compact Structure and Attractive Design: The design is user-friendly and convenient.
- Smooth Operation and Low Noise: It operates quietly, enhancing user comfort.
- Superior High-Temperature and Lubrication Performance: The bearings and gearboxes are positioned away from the housing, improving performance under high temperatures.
- Custom Design: We can create designs tailored to your specific requirements.
- Lubrication Maintenance: Each valve is filled with special lubricants before leaving the factory. Regular checks for lubrication are recommended.
Star discharge valves are commonly used in pneumatic conveying systems. They supply materials uniformly and continuously to the conveying pipe. This ensures stability for gases and solids within the pneumatic transport system. Additionally, they isolate pressure in the valve’s upper and lower sections, achieving a locking effect. Therefore, the star discharge valve is essential for pneumatic conveying systems.
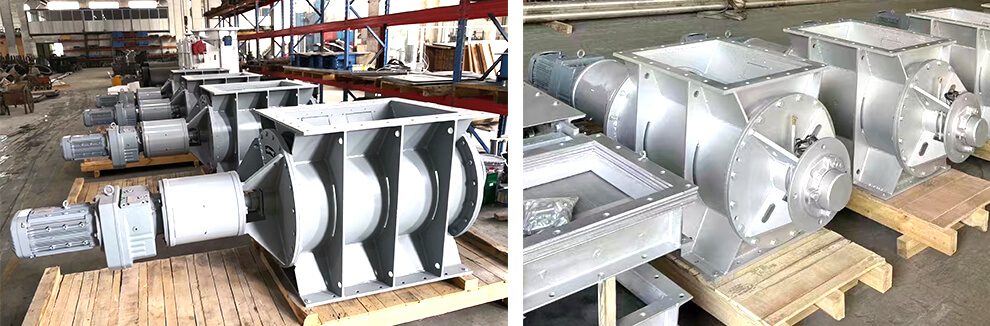
Applications of Star Discharge Valve
Star discharge valves serve as unloading devices in material collection systems, particularly for silos. They rank among the most advanced unloading devices available today. These valves are commonly used in dust removal systems and are especially suitable for dust and small particle materials. Industries such as environmental protection, metallurgy, chemicals, food, cement, road construction, and drying equipment favor star discharge valves for various projects.
Selection Guide for Star Discharge Valves
Choosing the right star discharge valve involves several key steps:
1. Define the Usage Location
Determine if the valve will be used indoors or outdoors. This choice influences protective measures.
2. Determine the Purpose of Use
Clarify if the valve will discharge materials in a metered, full-volume, or air-locking manner. This helps select the appropriate model.
3. Specify the Material Flow Rate
Understand the valve’s hourly flow rate. Specify whether the discharge is metered or variable to select the right capacity.
4. Define the Conveying Method
Classify the type of conveying: pneumatic or gravity flow. Clarifying this helps in selecting the correct valve.
5. Understand the Conveyed Material
Know the material characteristics and the pressure difference between the inlet and outlet flanges of the blower. This knowledge aids in determining the valve’s material and structure.
6. Analyze Material Properties
Consider properties like material name, particle size, true density, bulk density, temperature, repose angle, moisture content, and viscosity. These factors will influence the valve’s selection and configuration.
7. Consider Special Requirements
If you need an acceleration chamber or exhaust chamber, specify the models required. Also, consider the manufacturer of the reducer motor and the protection level.
8. Material Selection
Different materials have specific requirements. For example, food processing and pharmaceutical industries often require stainless steel star discharge valves due to their corrosion resistance and durability at high temperatures.
9. Safety Performance
Ensure safety and ease of operation by selecting reliable brands and models known for stability.
By following these steps, you can effectively choose a star discharge valve that meets your needs, ensuring stable operation and high performance in your production process.
Conclusion
In summary, selecting the right star discharge valve is crucial for efficient operation in your material handling systems. If you seek high-quality valves, Darko offers a range of reliable options tailored to your needs. For any inquiries or to discuss your specific requirements, please contact us. We are here to help!